The most important part of the pump is the 'drive pipe'.
Here is a view down it's 60' length. In spite of the way it
looks in this photo, it's actually pretty straight. One can
see a section of the 6' of plastic pipe going to the stand pipe
which I mention on another page.
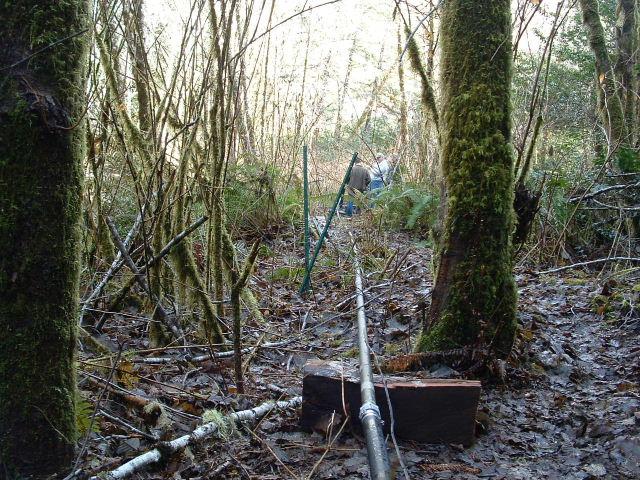
Note: Rigitity is the most critical aspect for good
performance. I've used 1 1/4 steel pipe which was scrapped
after being pulled from a well. I forgot or never knew what
gauge...schedule 40 maybe? In theory (mine), it actually
shouldn't matter a whole lot whether it bends or not, but a
bent drive pipe will be difficult to secure and thus, should be
avioded.
Note: This pump is actually quite loud. The noise is
a metalic clank that seems to emenate from every point on the
drive line. It got louder when I secured the pump to the
block of concrete mentioned below. If the noise proves to be
offensive at some point, I will bury the drive line.
Here is a picture of the pump in operation. The valve has just
snapped shut. I had access to some very nice stainless steel
fittings and happily, an industrial check valve that someone
had obtained from Wearhauser's scrap yard 20 years ago. Almost
everything you see here is stainless and of heavy gauge.
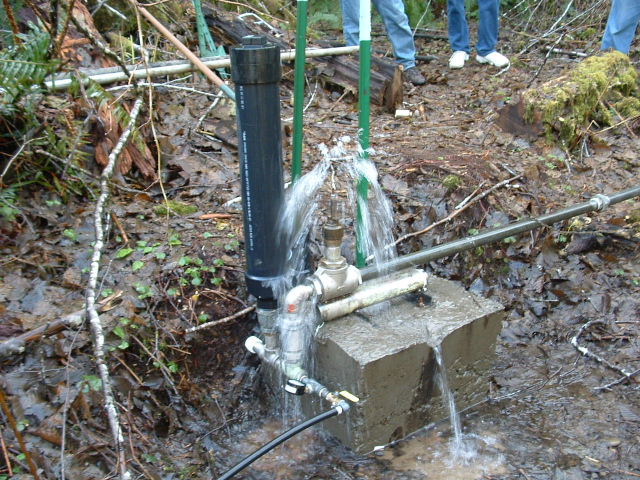
Note_1: The reason for the configuration is that I wished
the check valve to be 'upside-down' so that pebbles and rocks
would be less likely to screw things up and I could flush them.
The upshot is that one may take liberties with whatever designs
one might happen across.
Note_2: Instead of an air bleed 'snifter valve', I have put a
wheelborrow inner-tube inside the bounce chamber. So far, so
good...the thing isn't too critical anyway as far as dimensions
go (my theory.) Even at the valve on the pump when it is
cracked to produce 60 psi of back pressure, I see no indication
of a pulsating delivery which surprised me.
Note_3: The valve and gauge have proven to be invaluable
as it is necessary to have quite alot of back pressure in order
for *my* pump to cycle. I partially close this valve and watch
the gauge (so I don't blow the pump up) when starting it if for
some reason the native 50 psi is not available (i.e., the line
to my tank is not full.)
I do not know why my pump requires so much back pressure. I
suspect it has to do with the rigidity of everything and/or the
plastic at the end of the drive pipe and/or the over-sized body
and too long neck to the valve and/or the hight of the stand-pipe.
Note_4 There is a huge amount of force generated by
the water-hammer in the drive pipe. It made the pump jump
around alot so I welded on a mounting bracket and poured a 700lb
block of concrete around a large boulder which I found under
the surface of the ground. That did the trick! Also, as I
mentioned, the pump got generally louder. My opinion is that
proper securing of the pump is second only in importance to
rigidity of the drive pipe.
Note_5 As for the preformance, I recently put over 1800
gallons of water in my tank in 24 hours, and the tanks is
somewhat over 110 feet above the pump. I've not measured the
waste rate, but a ratio of 1/5 is expected for an efficient
pump if I recal correctly. I'm curious now, and will measure
the waste flow rate when I get a chance. BTW, the cycle
frequency of my pump seems to be more than once per
second...download the movie clip if you like.
750K Movie Clip if you like.
Lengthening the drive pipe from 40' to 60' didn't change the
frequency as much as I expected.
Update: I got around to measuring the waste. It's
around 6 gal/min. This makes it slightly better than 1/5
at it's current state of tune and workload.
My valve design differs somewhat from other descriptions I've
seen, but I'm happy with it. I had three worn out foot valves
from the former (traditional) water system to choose from when
making this one.:
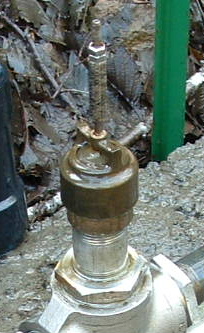
Note_1 I replaced the valve stem by sawing off the
original and carefully drilling and tapping the disk. The new
stem is a high quality stud which does not have threads where
it goes through the support. Under the disk, I screwed on a
second nut and set the threads with a punch. I wanted plenty
of weight so I left the stud long and took up the slack with a
tight fitting bit of fuel line hose (which is camoflauged in
this picture.) The double-nut on the top allows me to adjust
how far the valve drops into the body (and thus, in theory, the
water flow needed to snap the valve shut), but I've not needed
to fool with it.
Update: After around 30 days of run-time, there is a noticable
amoung of wear where the valve stem goes through the support.
Steel-on-brass, and the brass is wearing. Apperently the stem slaps
the guide as the valve seats with enough side-force that it is wearing.
Next I'll try either a gas engine valve guide or a teflon insert
depending on what I can fit to the valve housing...unfortunatly
there is little extra material on the foot-valve bodies that I
have kicking around.
Note_2 Note that the valve is actually sucked open with
some force by a 'reverse wave' in the drive pipe. This creates
stresses to be aware of and is a failure mode for some pumps and
can cause noise. In my system, the fuel line hose slipped over
the stem reduces both of these problems. The drive-pipe clank
noise is much louder than the clack valve in my pump.
Back